The packing box and packing method for aluminium coil and foil rolls shall be selected according to the product specification and size. For box type packing, the aluminum rolls can not be damaged after being packed. Materials for making the packing box can be wood board, multi-layer board, fiberboard, metal and other materials. The packing box shall be clean and orderly, with enough strength to ensure no deformation or damage during storage and transportation. The nails in the wooden packing box shall be arranged step by step, the nail tip shall not be exposed, and the nails shall be turned upside down to prevent the aluminum foil rolls from being hit by the cap and nail tip during transportation. The height of the bottom bracket shall meet the requirements of forklift transportation. After aluminum coil foil products pass the inspection and are sealed with inspection stamp, a layer of strong neutral or weak acid material shall be wrapped outside, and the joint shall be sealed with a tape or label.
The end face of the package is padded to protect the end face of the aluminum coil rolls. Add dry explosive, cover the material bag, plug the part of the two ends of the material bag beyond the aluminum record into the tube core, seal it with a suitable material head and put it into the packing box. After the product is packed, a layer of anti Lake paper or material cloth shall be covered on it. After the packing list is placed, it can be covered and sealed with steel belt. The steel belt shall be tied in a circle.
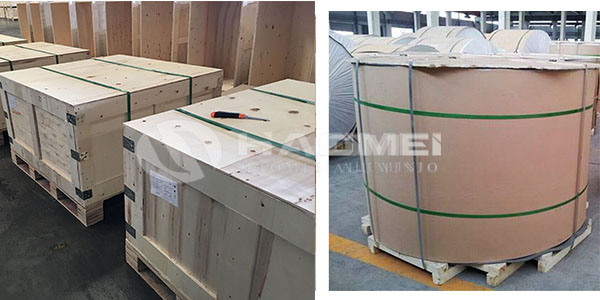
Conventional packaging for aluminium foil or coil rolls: for aluminum roll with a thickness of more than 0.05mm and a hard state every day, it can be packed with a tripod, and its packaging shall meet the requirements of transportation. The well frame is made of wood, and the upper and lower parts are made of two battens respectively. The height of the lower battens shall meet the requirements of the next train operation. The upper battens shall be made of arc shape corresponding to the roll radial direction. The upper and lower battens shall be fixed with poles, and the length of the poles shall be lower than the surface of the upper battens to complete the aluminum burn.
Firstly, a layer of strong neutral or weak acid material (generally high release) shall be placed on the outside of the aluminum foil rolls, and the packing list shall be placed, and the lap joint shall be firmly adhered with adhesive tape. A soft pad is placed on the end face to protect the end face of the aluminum foil roll.
Secondly, add dry explosive, wrap the whole material roll with the whole plastic cloth, the outer layer of the lap joint should be expected to have the material cloth mouth downward and be firmly stuck with adhesive tape, and plug the redundant parts at both ends of the plastic cloth into the pipe core. Finally, the rainproof cardboard with the same size is used to wrap the entire aluminum coil and seal the two ends along the circumference direction, and the joints between the end face and the circumference and all the gaps are firmly bonded with adhesive tape. Put the wrapped aluminum foil on the derrick and fix it with steel belt along the circumference direction, which shall be tied firmly. Put a box plate on the end face of the packed aluminum foil roll. In addition to the load-bearing and packaging costs of boxes and trellis, the transportation mode and the transportation and handling capacity of users should also be considered. Generally, the packaging weight of each aluminum coil of our company is 2.6 tons.
Export packaging method of aluminium coil suppliers: aluminum coil is a product with large export volume. The export packaging is usually in the form of plain well frame, the external part is fixed with steel belt, the external part of aluminum coil is provided with double-layer rainproof cloth, the internal part is moisture-proof, and the sealed packaging is adopted, which is suitable for sea transportation.